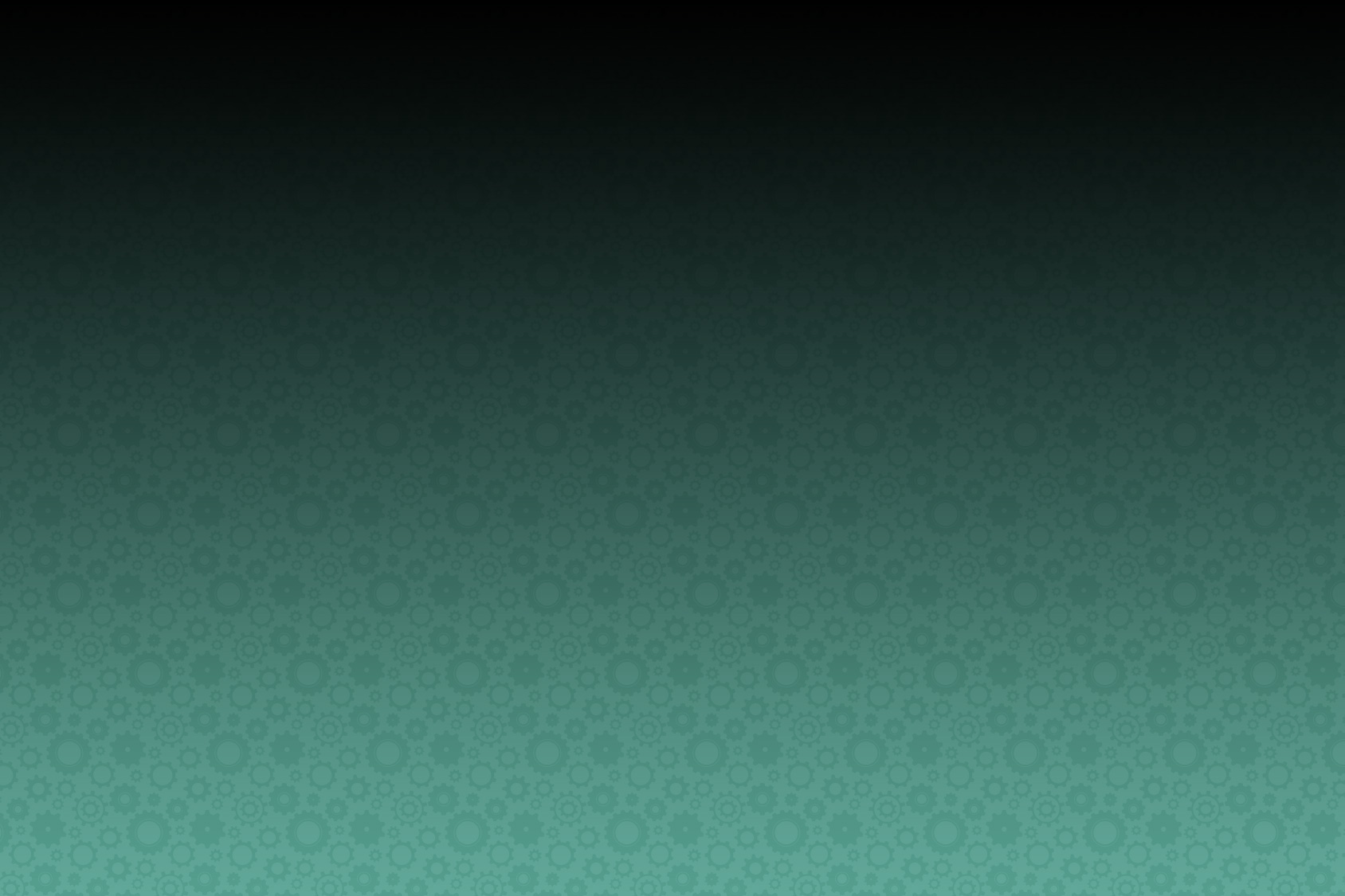
Metoda 5S
Przedsiębiorstwa bardzo często borykają się z problemem standaryzacji, np. podczas wdrażania nowego pracownika na stanowisko.
Zazwyczaj stosowane są szkolenia teoretyczne, po czym pracownik obejmuje dane stanowisko, lecz w rzeczywistości zanim pracownik w pełni zacznie pełnić swe obowiązki, musi się zaznajomić ze specyfiką danego zakładu, przyzwyczajeń współpracowników do wykonywania pewnych czynności, które są znane tylko dla nich.
Dla nowego pracownika jest to dużym problemem, gdyż nie jest w stanie w przeciągu kilku dni zaznajomić się z wszystkimi przypadkami. „Wsiąkanie” pracownika może potrwać nawet pół roku, w zależności od stanowiska i zakresu obowiązków. Odpowiedzią na ten problem jest standaryzacja pracy, m.in. za pomocą 5S- metoda ta wiąże ze sobą 5 kroków:
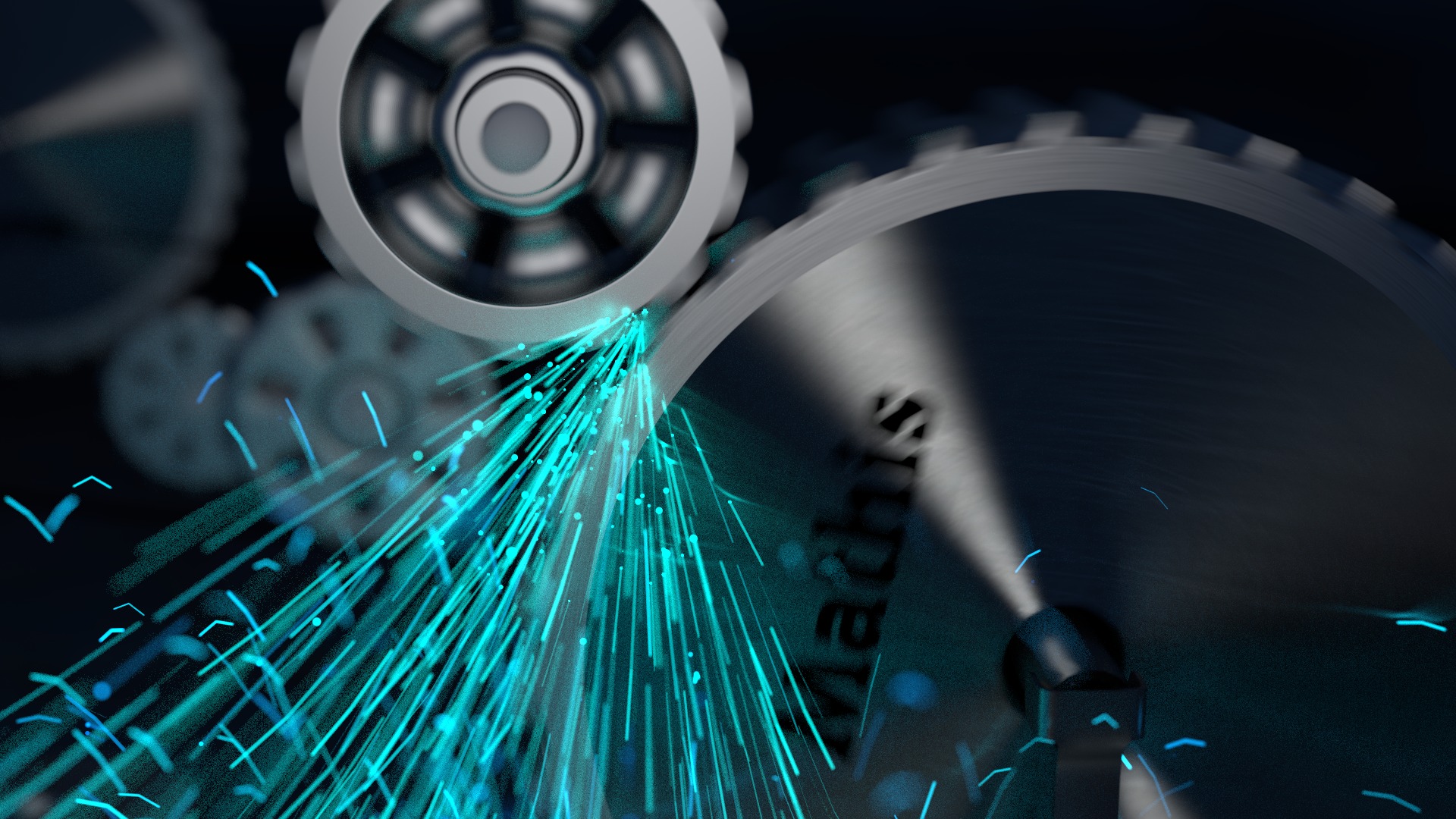
Systematyka
Sprzątanie
Standaryzacja
Samodoskonalenie
Wszelkie metody zostały opracowane przez japońskie zakłady produkcyjne Toyoty i są to jedynie wytyczne, a nie obligatoryjne zasady. Należy zawsze pamiętać, że inny rejon świata to inni ludzie, inna mentalność i inne problemy, dlatego nie należy wszystkich metod bezpośrednio powielać. Warunkiem sukcesu jest umiejętne dostosowanie ogólnych metod do danych warunków, jakie zespół napotyka w przedsiębiorstwie, co może oznaczać pominięcie niektórych kroków lub stworzenie własnych, dopasowanych do sytuacji.
W metodzie 5S pierwszym krokiem jest selekcja – pod tą nazwą kryje się ocena dotychczasowego funkcjonowania stanowiska. Osoba odpowiedzialna za dane stanowisko powinna wyznaczyć przedmioty, które w rzeczywistości są wykorzystywane na stanowisku, a które z nich jedynie znajdują się na stanowiskach. Kolejnym krokiem może być podział na przedmioty często i rzadko używane. Aby podział był widoczny od razu, najlepiej stosować metody wizualizacji, np. naklejki o różnych kolorach, gdzie kolor czerwony może oznaczać przedmiot niepotrzebny, pomarańczowy rzadko używany, a zielony często używany.
Następnym krokiem jest systematyka, w efekcie której przedmioty zostają podzielone w taki sposób, aby były widoczne dla każdego użytkownika stanowiska. Najczęściej stosowane sposoby, to tablice cieni, które odwzorowują kształt narzędzi poprzez zaniżenie materiału np. w gąbce. Innym przykładem tablicy cieni może być kombinacja kolorów, czyli przekopiowanie konkretnego narzędzia w postaci zdjęcia lub ręcznego rysunku na tablicę w miejscu, gdzie te narzędzie wisi, bądź leży.
Krok trzeci to sprzątanie, a nazwa tego kroku odnosi się bezpośrednio do działania. Przedsiębiorstwa wysoko wyspecjalizowane doszły do etapu, w którym każda czynność jest przydzielona konkretnej osobie, żeby każdy mógł najlepiej wykonywać swój zakres obowiązków. Problemem takiego schematu jest niedostosowanie jakości usług oraz czas oczekiwania na daną usługę. Oznacza to, iż np. stanowisko ślusarskie nie jest posprzątane, znajdują się na nim opiłki metali, wióry drewniane oraz bezpośrednio przy imadle leżą narzędzia. Takie stanowisko zastał pracownik po skończonej pracy, który obsługiwał je podczas tygodniowego urlopu kolegi, który właśnie wraca do pracy. W takim przypadku może się okazać, że nie znajdzie wszystkich narzędzi, ponieważ mogą być przykryte przez odpady pochodzące z procesu obróbki. Pracownik zaczyna poszukiwać wszystkich narzędzi i odkrywa, że jedno z nich jest złamane. Po oczyszczeniu stołu z opiłków i wiórów okazuje się, że przewód hydrauliczny przecieka i skrapla się olej. Po chwili dowiaduje się, że u kolegi z sąsiedniego gniazda praska hydrauliczna nieodpowiednio działa. Szybko znajdują odpowiedź dlaczego… Odpowiednie posprzątanie stanowiska pozwala wykryć natychmiast około 80% problemów.
Krokiem kolejnym jest standaryzacja, czyli przedstawienie wszystkich zmian w sposób jasny i zrozumiały dla każdej osoby. Dobrze opracowany standard jest zrozumiały przez osoby nie zajmujące się danym zagadnieniem, np. standard kończenia pracy na stanowisku do cięcia laserowego – po zaproszeniu na dane stanowisko księgowych powinni wykonać wszystkie kroki po kolei bez przeszkód. Bardzo trudno jest opracować standard przez osoby, które codziennie znajdują się na bieżącym stanowisku, ponieważ dla takiej osoby wszystkie kroki są oczywiste i nie będzie widziała potrzebny umieszczania ich w standardach. Najczęściej stosowaną praktyką jest kontrola schematu przez osobą zupełnie niezwiązaną z danymi czynnościami, dlatego tak ważne jest stosowanie wizualizacji.
Ostatnim krokiem jest samodoskonalenie, często zamiennie stosowane jako samodyscyplina. Jest to punkt całej drogi, który fizycznie już nam nie zmienia wyglądu stanowiska oraz nie poprawia ergonomii pracy, a pozwala na utrzymanie wprowadzonego ładu. Jeśli jakiś pracownik wewnętrznie nie będzie zmotywowany do podtrzymania zmian, to gwarantowane jest powrót do stanu poprzedniego. W tym miejscu dużą rolę pełnią osoby, które dbają o prawidłowe wdrożenie 5S. Doświadczenie w wielu zakładach pokazuje, iż pośpiech jest gwoździem do trumny dla całego projektu, więc zachęcamy spokojne wprowadzać wszelkie metody, w połączeniu ze ścisłą współpracą ludzi.